INDUSTRY INFO
PALLET WRAP INFORMATION
differences between blown & cast stretch films

BLOWN STRETCH FILM
- MANUFACTURING PROCESS:
- Process: Created by melting resin and extruding it through a circular die. The film is then blown into a bubble, cooled by air, and collapsed into flat film.
- Cooling: Slower cooling process, leading to more crystalline structure.
- Orientation: Bi-axial orientation (primarily in the machine direction)
- PROPERTIES:
- Clarity: Generally, less clear and glossy due to the slower cooling process.
- Strength: Higher puncture and tear resistance because of the crystalline structure.
- Elasticity: Better memory, meaning it retains its stretch and cling properties longer.
- Noise: Noisier to unwind due to the structure.
- Cost: Typically, more expensive due to the complex manufacturing process.
- APPLICATIONS:
- Ideal for: Securing irregularly shaped loads, handling heavy-duty wrapping needs, and providing protection for long-term storage.
- Preferred for: Products requiring higher puncture resistance and better load retention over time.

CAST STRETCH FILM
- MANUFACTURING PROCESS:
- Process: Produced by melting resin and extruding it through a slot die, then cooling it on chilled rollers.
- Cooling: Faster cooling process, resulting in a more uniform film.
- Orientation: Uni-axial orientation (primarily in the machine direction).
- PROPERTIES:
- Clarity: Higher clarity and gloss, making it more transparent.
- Strength: Lower puncture resistance compared to blown film.
- Elasticity: Less memory, which means it can lose cling properties faster.
- Noise: Quieter to unwind because of the smoother surface.
- Cost: Generally, less expensive due to the simpler manufacturing process.
- APPLICATIONS:
- Ideal for: Wrapping uniform loads, lighter-duty applications, and when high clarity is needed.
- Preferred for: Products requiring better visual inspection, quieter application, and lower cost.
SUMMARY TABLE:
FEATURE: | BLOWN STRETCH FILM | CAST STRETCH FILM |
Manufacturing Process | Blown into a bubble, slow cooling | Extruded through a slot die, fast cooling |
Clarity | Less clear | High clarity and glossy |
Strength | HIgher puncture and tear resistance | Lower puncture resistance |
Elasticity | Better memory | Less memory |
Noise | Noisier to unwind | Quieter to unwind |
Cost | More expensive | Less expensive |
Ideal For | Irregular loads, heavy-duty, long term | Uniform loads, lighter-duty, high clarity needed |
Preferred For | Higher puncture resistance, load retention | Visual inspection, quieter application cost |
This comparison should help you understand the key differences between blown and cast stretch films and determine which type is best suited for your specific needs.
WRAPPING MACHINE INDUSTRY STANDARD PROFLE
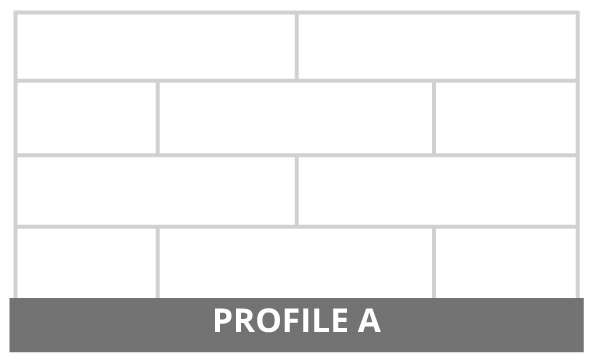
PROFILE A
A pallet load with load footprint the same size as the pallet, with uniform shape and no protrusions

PROFILE B
A pallet load with load footprint different to the size of the pallet with the load slightly irregular shaped
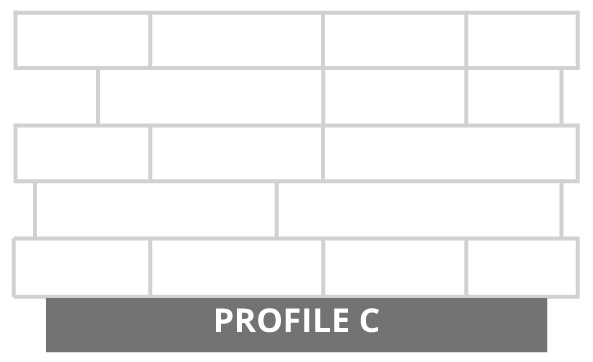
PROFILE C
A pallet load with load footprint significantly different to the size of the pallet with the load highly irregular with sharp edges
differences between manual , semi-automated & fully-automated
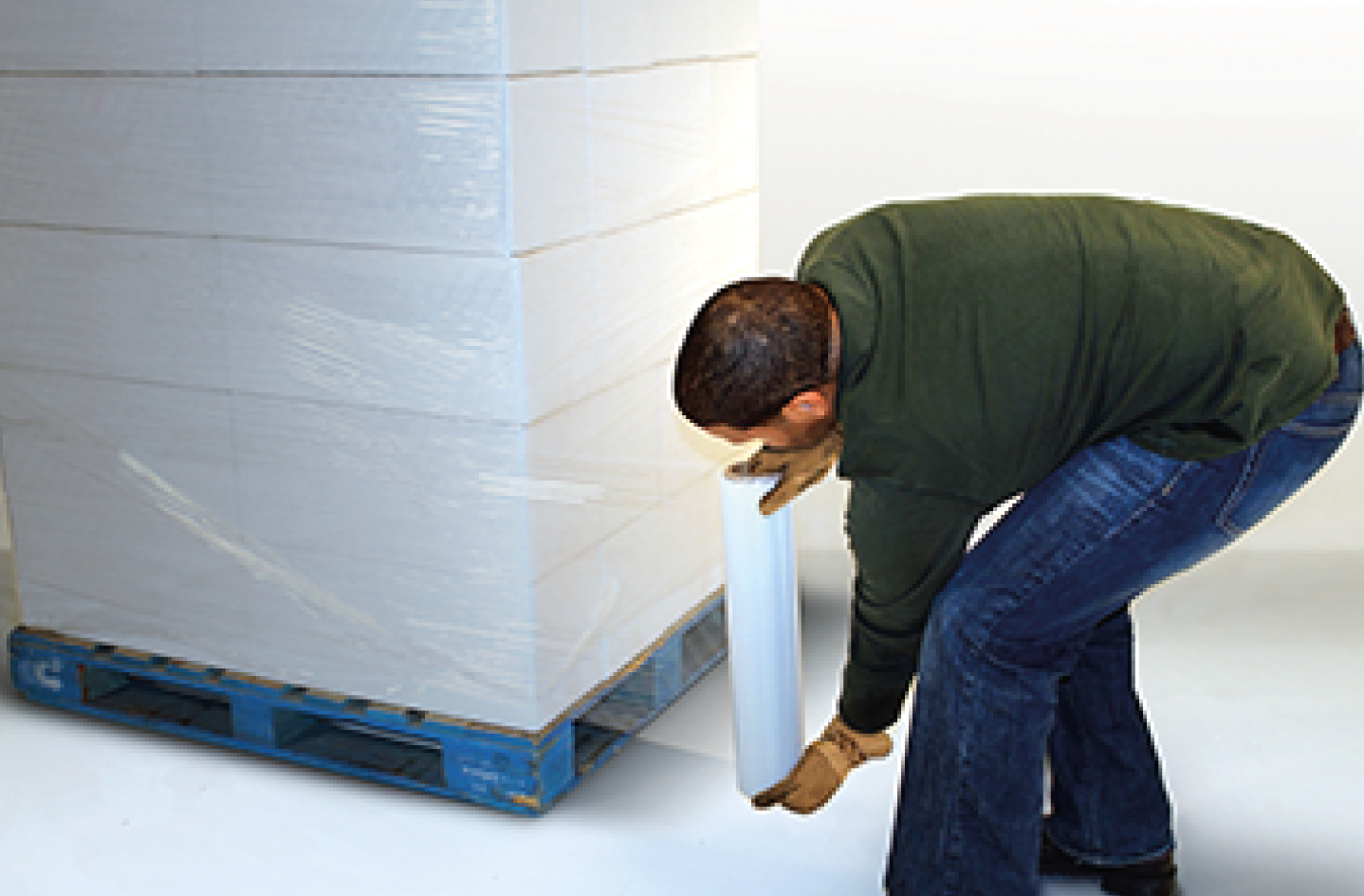
MANNUAL WRAPPING
- THROUGHPUT: Limited by ability of labour
- PROFLE A: Suitable
- PROFILE B: Suitable
- PROFILE C: Suitable
- FLEXIBILITY: Highly flexible
- CONSISTENCY OF APPLICATION: Wrapping pattern dependant on operator
- FILM DAMAGE & WASTE: High
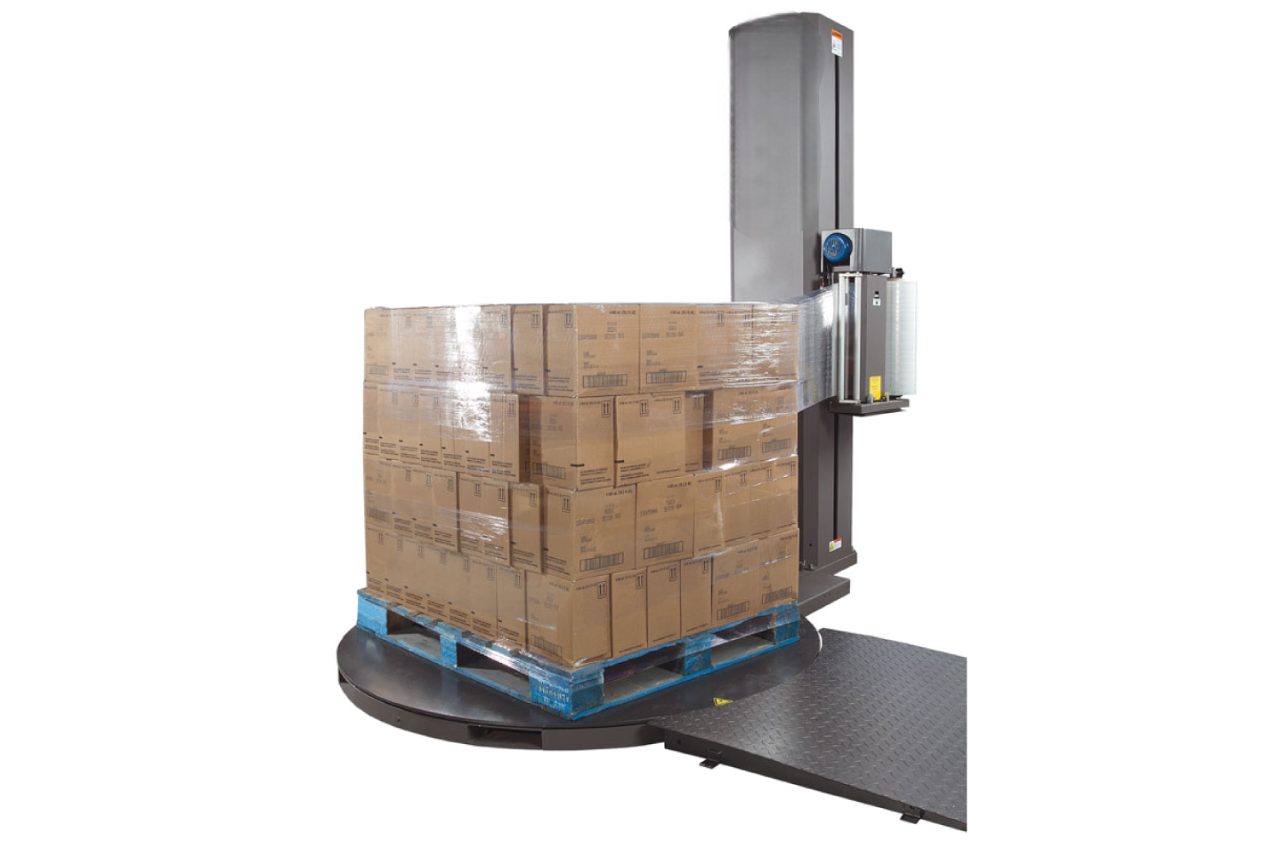
SEMI-AUTOMATIC WRAPPING
- THROUGHPUT: Cost effective in most throughputs
- PROFLE A: Suitable
- PROFILE B: Suitable
- PROFILE C: Not recommended
- FLEXIBILITY: Flexible
- CONSISTENCY OF APPLICATION: High
- FILM DAMAGE & WASTE: Low

FULLY-AUTOMATED WRAPPING
- THROUGHPUT: Requires large throughput
- PROFLE A: Suitable
- PROFILE B: Suitable
- PROFILE C: Not recommended
- FLEXIBILITY: Inflexible
- CONSISTENCY OF APPLICATION: High
- FILM DAMAGE & WASTE: Low
BLACK MULCH INFORMATION
How Mulch Plastic Supports Organic and Eco-Conscious Farming
With rising pressure to produce food more sustainably, South African farmers are increasingly looking for ways to grow crops efficiently while staying environmentally responsible. In organic and eco-conscious farming, every input matters — and one of the most effective tools available today is mulch plastic, also known as plastic mulch film.
Although biodegradable mulch films are gaining attention, they remain costly and often fall short in durability and performance. At Polywrap, we offer a more accessible, long-term solution: Virgin or recyclable LDPE mulch plastic — a practical choice that helps farmers reduce chemical usage, conserve water, and enhance crop yields while still aligning with eco-wise farming principles.
What Is Mulch Plastic?
Mulch plastic is a thin layer of film — usually black, clear, or white — that is laid over the soil surface in planting rows. It plays a crucial role in moisture retention, temperature regulation, and weed control, making it a staple in modern agriculture, including organic farming systems.
Polywrap’s mulch plastic is made from low-density polyethylene (LDPE), a strong and flexible material that can be recycled after use. While it is not biodegradable, when managed responsibly, it remains a sustainable option that significantly reduces environmental impact
7 Key benefits of mulch plastic in Sustainable & Organic Farming
Natural Weed Suppression
Mulch plastic acts as a barrier, blocking sunlight from reaching the soil. This naturally prevents weed growth, eliminating the need for herbicides — a major win for organic farms where chemical use is restricted or not allowed.
Water Conservation
One of the biggest challenges in South African agriculture is water scarcity. Mulch film drastically reduces surface evaporation, helping the soil retain moisture. Farmers often report reduced irrigation requirements, saving water and lowering input costs.
Improved Soil Temperature
Black and clear mulch plastic helps warm the soil earlier in the season, promoting faster germination and better root development. This leads to stronger, healthier crops with earlier and more uniform yields.
Cleaner Produce, Less Waste
By keeping fruits and vegetables off the soil, mulch plastic reduces the risk of soil-borne diseases, rot, and dirt contamination. This results in cleaner produce and higher marketable yields, especially in crops like tomatoes, peppers, strawberries, and melons.
Erosion Control & Soil Protection
Wind and rain can erode precious topsoil, especially in uncovered fields. Mulch film protects the soil surface, helping preserve its structure and minimise nutrient runoff.
Pest Reduction
Mulch plastic acts as a physical barrier between the soil and crops, making it harder for soil-dwelling pests to reach plants. Reflective or coloured films can also deter certain insects, contributing to natural pest control without the need for synthetic pesticides.
Fully Recyclable
Unlike biodegradable alternatives that often break down inconsistently or require specific composting conditions, LDPE mulch film can be collected, baled, and recycled into new plastic products. This means that when handled responsibly, your plastic footprint is reduced — without compromising performance.
Is Mulch plastic really eco-friendly?
It’s a fair question. While not biodegradable, mulch plastic becomes eco-friendly when used correctly:
- It reduces reliance on water, fertiliser, and chemicals.
- It boosts resource efficiency by improving yields per hectare.
- It is recyclable, especially when farmers and cooperatives organise proper collection after the season.
With the growing interest in circular agriculture, many farmers are seeing mulch film as a long-term eco-practical solution — especially when biodegradable options are out of budget or not yet viable.
MACHINE WRAP ROLLS 400MM WIDTH
- THICKNESS OPTIONS : 13, 15, 17, 20, 23, 25, 27
- LENGTH OPTIONS : 1500, 2000, 2500, 3000
*Contact us for more information
APPLICATION ACROSS CROPS
Mulch film is used across a wide range of crops in South Africa, including:
- Vegetables: Tomatoes, peppers, cabbage, butternut, pumpkins, onions, spinach, and carrots
- Fruits: Strawberries, melons, cucumbers
- Herbs and niche crops: Basil, coriander, chillies, and more
Our LDPE mulch film is available in various widths, lengths, and microns to suit smallholdings, tunnel farming, and commercial operations alike.
THE POLYWRP PROMISE
At Polywrap, we work closely with farmers to supply cost-effective, reliable, and recyclable farming plastics that enhance productivity and support long-term sustainability. While we don’t currently offer biodegradable mulch film, our LDPE products are designed with eco-conscious farming in mind.
Whether you’re planting for the local market or exporting organic produce, Polywrap’s mulch plastic gives you a head start towards greener farming.

SHRINK WRAP INFORMATION
Shrink Wrap That Works Smarter: Eco-Conscious, Food-Safe, and Cost-Effective Packaging from the Western Cape
In today’s packaging world, the pressure is on: brands must cut costs, reduce plastic waste, and comply with food safety standards — all without compromising performance. At Polywrap, we’re proud to offer locally manufactured shrink wrap that meets these needs head-on.
As one of the oldest shrink film manufacturers in the Western Cape, we’ve helped thousands of businesses across South Africa and neighbouring countries protect their products with reliable, cost-effective, and environmentally conscious shrink film — proudly made for the Southern African market.
MACHINE WRAP ROLLS 400MM WIDTH
- THICKNESS OPTIONS : 13, 15, 17, 20, 23, 25, 27
- LENGTH OPTIONS : 1500, 2000, 2500, 3000
*Contact us for more information
WHY CHOOSE POLYWRAP SHRINK WRAP ?
- Food-grade and FSCC certified
- Contains recycled content – contributing to circular packaging
- Cost-efficient without compromising quality
- Made in South Africa – fast turnaround and reduced supply chain risk
- Polyco member – committed to sustainable plastic packaging
- SADC registered – easy cross-border trade into neighbouring countries
- Trusted by leading South African brands
Shrink Wrap That Supports Your Sustainability Goals
We understand that packaging is under the spotlight — and we’ve responded with solutions that help brands shrink their environmental footprint.
Our shrink wrap is made from LDPE (Low-Density Polyethylene) and is 100% recyclable. We also offer a range of options containing post-consumer recycled (PCR) content, helping your business meet eco-packaging targets without increasing costs.
Eco Benefits of Our Shrink Film:
- Available in blends containing recycled content
- Manufactured using low-waste extrusion processes
- 100% recyclable where collection infrastructure exists
- Designed for source reduction – use less plastic to do more
- Reduces the need for outer packaging like boxes
Food-Grade Approved for Safe, Clean Packaging
Food manufacturers and beverage producers across the Western Cape and beyond trust Polywrap for shrink film that’s clean, strong, and compliant. Our FSCC certification ensures our products meet strict food safety standards, making them ideal for:
- Bottled water and beverage multipacks
- Canned goods and trays
- Dairy and yoghurt products
- Frozen foods and boxed meat
- Fruit and vegetable trays
We work with some of South Africa’s most recognised food brands — a testament to our reputation for quality and consistency.
Shrink Your Costs Without Shrinking Performance
When it comes to cost savings, our shrink wrap is designed to help you do more with less. We offer:
- Right-gauged films to reduce thickness and material use
- Optimised roll lengths and widths to minimise waste
- Tailored solutions for manual and automated applications
- Local support with fast lead times and competitive pricing
And because we manufacture locally in the Western Cape, you benefit from more stable pricing, faster delivery, and direct access to technical expertise — no import delays or inflated overseas costs.